Es ist an der Zeit, es besser zu machen.
Warum ein Dorftischler aus dem Waldviertel eine Geschichte über „Lean am Bau“ erzählen kann.
„Lean am Bau“ wurde in den vergangenen Jahren immer mehr zum Thema. Bei uns gibt es diese Denkweise bereits seit fast 20 Jahren und wir haben in diesem Zeitraum viel Lernerfahrung gesammelt.
1. Zum Unternehmen
Im nördlichen Niederösterreich, unweit der tschechischen Grenze, am Rand der Marktgemeinde Vitis, ist das Unternehmen Schrenk zu finden. Wir sind ein typisches Familienunternehmen, das 1977 von Franz Schrenk als klassische Tischlerei gegründet wurde. Schon bald beschäftigten wir uns hauptsächlich mit der Herstellung von Treppen und Innentüren und konnten rasch, aber dennoch organisch, wachsen. 2010 wurde der Generationswechsel vollzogen, und seither führt Stefan Schrenk überaus erfolgreich und höchst innovativ die Geschäfte.
Bei Schrenk wird bei allen Aktivitäten im Unternehmen ein KVP (kontinuierlicher Verbesserungsprozess) angewandt. Das Credo lautet: „Deshalb reden wir drüber“. Mit der starken Einbindung der Mitarbeitenden, die ja in der ersten Reihe stehen und Herausforderungen am schnellsten erkennen, wird die Qualität stetig verbessert. Und zwar nicht nur die Qualität des Endproduktes, sondern auch die der Arbeitsabläufe und der Unternehmensprozesse bis hin zur Qualität und Stabilität der Marke Schrenk.
Über die Zeit hat sich der Fokus in der Firma verschoben: Der klassische, monetäre Erfolg rückte von ganz oben in einen untergeordneten Rang. Wir haben Agilität, Wandlungs- und Lernfähigkeit in den Fokus gerückt und die Organisation darauf ausgerichtet. So hat sich das Unternehmen in eine Richtung entwickelt, die als Nebenprodukt Kosten gesenkt und Ressourcen freigesetzt hat. Synergien wurden nicht nur entdeckt, sondern auch genutzt, die Mitarbeitenden sind motivierter, zufriedener und machen deutlich weniger Fehler.
In jüngster Zeit hat sich Schrenk raus aus der optimierten Werkshalle und rein in die zu optimierende Baustellenwelt begeben. Mit der „Lean Works GmbH“ wurde ein eigenes Unternehmen gegründet, in dem beispielsweise Fertigungslinien für innovative Produkte entwickelt werden. Prämissen dabei: kurze Durchlaufzeit, Agilität und Wandlungsfähigkeit aufgrund von schwankenden Auslastungen, und dennoch hohe Effizienz. Der Clou: Diese Fertigungslinien wurden zur Gänze von den Mitarbeitenden selbst entwickelt. So ist etwa eine Fertigungslinie für Holzaußenwände eines modular veränderbaren Hauses entstanden. Doch damit nicht genug. Das Team hat den gesamten Prozess im Auge und deshalb zum Beispiel auch die Montage analysiert, um noch gezielter, besser, kreativer und schneller arbeiten zu können. Dadurch wurde ein System entwickelt, mit dem eine fünfköpfige Mannschaft ein solches Haus von der „grünen Wiese“ in fünf Tagen einzugsfertig montiert und komplett einrichtet, inklusive der modernsten Haustechnik.
Ein weiteres Kapitel in der Unternehmensgeschichte wird aktuell mit WoodRocks geschrieben. Die WoodRocks Bau GmbH wurde gemeinsam mit dem Vorarlberger Bauunternehmen Rhomberg gegründet und wird mehrgeschossige Wohnhausanlagen im Holz-Systembau errichten. Ziel ist es, durch eine hohe Vorfertigung und einer organisierten Baulogistik eine Bauzeit von nur wenigen Tagen zu erreichen.
2. Beginnen wir am Ende
Prozesse sind immer von hinten zu planen und zu optimieren. Nur wenn man die Erwartungen am Ende ganz genau kennt, kann man alle Schritte richtig setzen.
Die Digitalisierung wird auch im Bauwesen ganz neue Wege der industriellen, automatisierten Vorfertigung ermöglichen. Das wird uns zu einer radikalen Optimierung unserer Prozesse zwingen, da wir sonst das Falsche digitalisieren. Und die, die das tun, werden nicht überleben. Die, die nichts tun, auch nicht. Positiv gesagt: Wer gemeinsam mit allen dafür erforderlichen Menschen die eigenen Prozesse optimiert und digitalisiert, wird erfolgreich sein. Alles ist natürlich relativ, optimal ist nie etwas. Daher ist Optimierung ein permanenter Prozess, der wiederum dauernd zu optimieren ist.
3. Zusammenhang Prozesse – Qualität, Termine, Kosten
Die herkömmliche Meinung ist, dass es teurer wird und länger dauert, wenn man die Qualität steigern will. Das ist falsch. Diese Meinung geht von der irrigen Annahme aus, dass man an den Prozessen, die üblicherweise nicht optimal ablaufen, nichts ändert.
Einige Beispiele:
Wenn man die am Prozess beteiligten Menschen gemeinsam an der Reduktion der Durchlaufzeit arbeiten lässt, kommt es zu Verbesserungen in allen Bereichen. Es ist hier wichtig, die reine Profitbetrachtung nicht auf den ersten Rang zu setzen. Nur eine wandlungs- und lernfähige Organisation kann so etwas schaffen.
In einem Prozess mit maximal kurzer Durchlaufzeit gibt es keine Puffer. Fehler kommen sofort an die Oberfläche und sind für alle Beteiligten sofort sichtbar. Somit kann unmittelbar an der Lösungsfindung und Behebung gearbeitet werden, wobei alle daran beteiligt sind. Das ist aber nur in einer Kultur, in der Fehler erlaubt sind, vorstellbar und, mehr noch, in der das Erkennen und Aufzeigen von Fehlern als Chance für alle erkannt wird.
Dieser Gedanke ist radikal, aber anders wird es nicht gehen – gerade am Bau mit unserer noch immer hohen Improvisationserfordernis.
Wenn Fehler frühzeitig erkannt werden, kommt Qualität bei den Kund:innen an. Schnelle Durchlaufzeit braucht eine sehr hohe Prozessqualität, daher bringt uns eine kurze Durchlaufzeit hohe Qualität bei hoher Liefertreue und verursacht dadurch nur geringe Kosten.
4. Zusammenhang Prozesse – Digitalisierung – Vorfertigung
Erst die Digitalisierung ermöglicht die industrielle Vorfertigung im Bauwesen. Wie andere Industriezweige zeigen, erlaubt digital unterstützte Vorfertigung hohe Individualisierung. Das ist für das Bauwesen hinsichtlich Gestaltung, Funktion und Nutzung essenziell.
Die Digitalisierung mit BIM, Benchmarking, Simulation, Variation, Visualisierung etc. lässt uns Fehler früher erkennen und ausmerzen – das gilt für Prozesse und Produkte. Will man vorfertigen, ist es entscheidend, dass das Produkt und der Prozess vorher weitgehend fehlerfrei gemacht bzw. geplant wurden. Die Vorfertigung erlaubt Automatisierung und damit wiederum Optimierung hinsichtlich Qualität, Termine und Kosten. Sie erfordert aber auch minutiös geplante Prozesse, insbesondere dann, wenn sie automatisiert ist, denn Roboter verzeihen im Gegensatz zu Menschen keine Prozessfehler. Es sei denn, wir haben sie dank künstlicher Intelligenz (KI) so „intelligent“ gemacht, dass sie unsere Fehler ausgleichen. Aber das wird noch dauern.
Prozessoptimierung bedeutet die Optimierung von Arbeitsfluss und Arbeitsplatz. Hier wurden neue Wege beschritten – es wurde jahrelang gemeinsam entwickelt und das darf niemals aufhören. Jeder Handwerker bekommt nach einem gemeinsam erarbeiteten Plan von einem Logistikteam das benötigte Material in entsprechender Qualität und stückgenau direkt an den Verarbeitungsort. Ganze Module mit komplizierter Technik werden im Werk unter optimalen Bedingungen hergestellt und verursachen daher einen sehr geringen Planungs- und Koordinierungsaufwand auf der Baustelle.
Einfache Prozesse brauchen wenig Regeln.
Beispiel von außen: Eine Ampelkreuzung muss mit komplizierter Steuerung geregelt werden. In einem Kreisverkehr werden die Beteiligten in den Prozess einbezogen und es braucht keine Steuerung mehr.
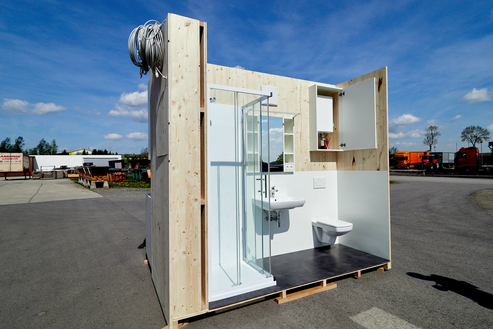
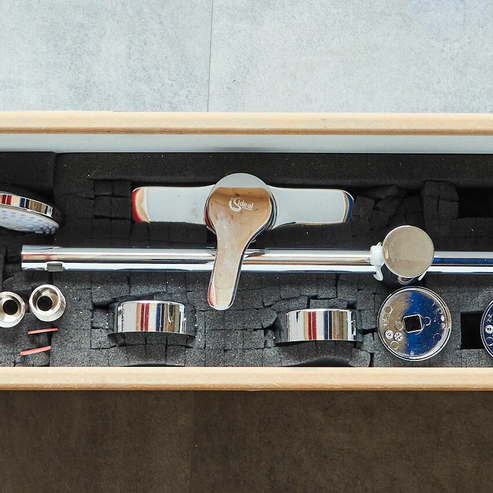
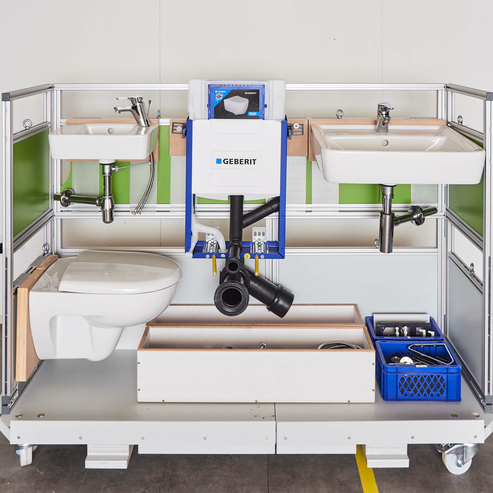
5. Prozesse von hinten aufzäumen
Jeder folgende Prozessschritt ist der „Kunde“ des vorherigen. Wir müssen somit beim allerletzten Prozessschritt beginnen, also den Bedarf feststellen und erfüllen, bevor wir den vorherigen planen. Die Optimierung von Prozessketten kann nur von hinten gelingen. Was wir damit meinen, kann anhand von LEGO sehr gut erläutert werden: Bei der ersten Prozessvariante werden alle Steine gemischt angeliefert und es gibt nur schlechte Information. Die Spieler:innen (die Personen am Bau, bei der Montage) brauchen Zeit und Geduld und es werden viele Fehler passieren. Bei der zweiten Variante ist die Materialandienung am Kundenbedarf orientiert, die Legosätze kommen also bereits vorab zusammengesetzt und in der richtigen Reihenfolge auf die „Baustelle“.
Die Logistik orientiert sich an den internen Kund:innen. Weiter zurück im Prozess orientiert sich die Fertigung an der Logistik. Am Ende orientieren sich die Planer:innen an den internen Kund:innen. Gefordert wird hohe Informationsqualität. Die Planer:innen sind Diener:innen der Wertschöpfung!
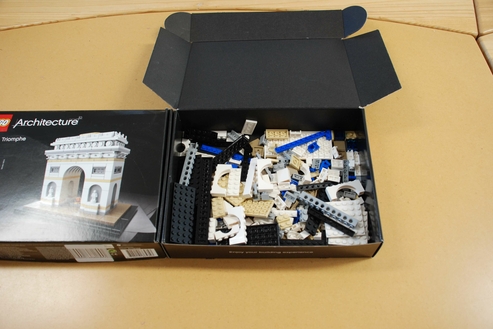
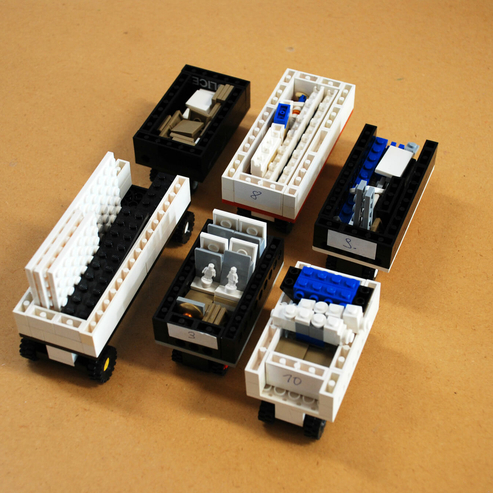
6. Vom Silodenken zum Ressourcendenken
Traditionell sind unsere Geschäftsprozesse in „vertikalen Silos“ aufgebaut: Anlieferung, Produktion, Montage, Vertrieb etc. In jedem Silo herrscht Silodenken, es wird jeweils der eigene Bereich optimiert. Dabei entsteht keine Gesamtoptimierung. Erst wenn wir alle Ressourcen in Summe gemeinsam betrachten und alle Prozesse gemeinsam so steuern, dass das Gesamtergebnis optimiert wird, sind wir auf dem richtigen Weg.
Beispiel für das Ressourcendenken:
Wenn der Einkauf seinen Bereich optimiert, denkt er in erster Linie an Preissenkung. Dies kann durch größere Bestellmenge erfolgen oder durch Veränderungen der Produkte – häufig in schlechterer Qualität. Der Einkauf optimiert durch größere Bestellmenge „seine“ Kosten, aber auf der Baustelle entstehen dadurch höhere Bestände. Die größeren Mengen benötigen mehr Platz und durch häufiges Umschlichten mehr Zeit, Beschädigungen und Schwund werden ebenfalls zunehmen. Durch schlechtere Qualität kommt es häufig zu Mehraufwand auf der Baustelle oder in der Fertigung. Dies wird aber meist nicht richtig gemessen und selten auf die eigentliche Ursache zurückgeführt. Silodenken im Einkauf führt in Summe zu Mehrkosten, die aber nicht der Kostenstelle Einkauf zugerechnet werden.
Die Kostenrechnung ist ein wesentliches betriebliches Steuerungselement, aber in der Praxis kennen viele von uns Fehlentwicklungen durch fehlgeleitetes oder fehlinterpretiertes Berichtswesen.
7. Der ruhige Fluss
Jede Wertschöpfungskette hat Engpässe, kritische Punkte, Irregularitäten im täglichen Betrieb. Je individueller die Elemente und Produkte sind, desto mehr dieser Engpässe und kritischen Punkte gibt es. Produziert man eine Million Mal das Gleiche, kann man vereinheitlichen. Das ist im Bauwesen nicht zu erwarten und bei KMUs schon gar nicht.
Es ist daher die Aufgabe, Prozessketten zu gestalten, die auf einen gleichmäßigen, ausgewogenen Fluss aller Ressourcen achten. Das betrifft Menschen, Material, Maschinen. Es hat keinen Sinn, einen Betrieb dahingehend zu optimieren, dass einige Maschinen optimal ausgelastet sind. Spürt man als Unternehmer diesen Zwang, sollte man eher darüber nachdenken, ob man in diese Maschine richtig investiert hat. Viel wichtiger ist es, dass Mensch und Material in ruhigem Fluss sind und in Summe möglichst effizient vom Rohstoff zum Endprodukt gelangen. Dann ersparen wir uns viel Hektik, Manipulation, Zwischenlagerung, Suche, Disposition, Reibung, Frustration …
8. Den Überblick bewahren
So weit wie möglich sollen die Mitarbeitenden den Überblick über die Produktionskette im Auge behalten können, denn nur dann sind Störungen rasch erkennbar und Verbesserungen ableitbar.
Lean ist „Gembaismus“
(Gemba = der Ort, wo es in Erscheinung tritt)
Alle am Prozess Beteiligten sind Diener:innen der Wertschöpfung und daher muss sich alles daran ausrichten, dort die besten Bedingungen zu schaffen. Hohe Produkt- und Informationsqualität ist gefordert. Die Logistik (Mizusumashi) nimmt hier eine entscheidende Rolle ein, denn sie dient die Materialien und Informationen an.
Die Planer:innen haben eine bedeutende Rolle. Denn es geht nicht nur darum, eine technisch richtige Lösung zu finden, sondern um „fertigungsgerechtes Engineering“. Daher müssen die Planer:innen ein hohes Verständnis für die Probleme in der Fertigung und Montage haben. (Die Japaner:innen beschreiben es so schön: Ein Techniker muss sich mindestens drei Mal am Tag die Hände waschen). :-)
In kleineren Betrieben kann das so organisiert werden, dass alle Prozessschritte in einer Halle stattfinden. Bei größeren, komplexeren Prozessketten sind dafür geeignete Wege zu finden. In der Treppenproduktion hatten wir früher acht Wochen Durchlaufzeit – also die Zeit, in der das Material vom Zuschnitt bis zur Auslieferung in der Werkshalle war. Heute sind es acht Stunden!
Bei einer langen Durchlaufzeit gibt es üblicherweise viele Bestände vor und nach den Maschinen, für den Einzelnen sind dadurch weder die Zusammenhänge noch die Probleme im Prozess erkennbar. Wenn ein Fehler an die Oberfläche tritt, der vor einigen Tagen in einem anderen Prozessschritt gemacht wurde, ist es oft schwierig, sich daran zu erinnern und die Ursache exakt zu eruieren. Bestände verdecken Fehler! Bei kurzer Durchlaufzeit treten Fehler hingegen sofort an die Oberfläche und sind für alle ersichtlich. Dadurch kann jeder an der Ursachenfindung mitarbeiten und eine schnelle Lösung finden, was sehr rasch in einer hohen Prozessqualität resultiert!
9. Flexibilität als Prinzip erkennen
Oft wird fälschlich Starrheit als Voraussetzung industrieller Fertigung gesehen. Konsequente Prozessoptimierung unter der Zielsetzung, immer dem Markt und den Geschäftsbedingungen folgen zu können, erfordert aber oft sehr rasche Anpassungsfähigkeit. Sowohl Mitarbeitende als auch Maschinen und Arbeitsplätze haben dem Prinzip der Flexibilität zu folgen. Natürlich gilt das nicht für die Massenfertigung, aber im Bauwesen und insbesondere in der mittelständischen Industrie, für Gewerbebetriebe in den Regionen wird hohe Flexibilität in den Prozessketten noch lange ein Thema bleiben.
Stabil ist das Unlebendige – das Lebendige ist dynamisch. Oberste Priorität eines Organismus (einer Organisation) sollte die Wandlungs- und Lernfähigkeit haben, um sich ständig weiterentwickeln und auf die permanente Veränderung reagieren zu können. Kurzfristiges und kurzsichtiges Kostendenken verhindern diese Lebendigkeit. Dies ist sicherlich einer der Hauptgründe, warum die Bauwirtschaft sich in den vergangenen 25 Jahren nicht wirklich weiterentwickelt hat. Die Arbeitsumstände werden immer schlechter, die Qualität und Produktivität sinken kontinuierlich. Dennoch wird in einigen Bereichen viel Geld verdient – leider in den falschen.
Ein Beispiel: Auf ruhigem Gewässer kann ein Ruderboot mit einem Steuermann, der das Kommando hat und den Takt vorgibt, sehr schnell gerudert werden. Im Wildwasser dagegen braucht es jeden Einzelnen, der selbstständig auf die sich ändernden Bedingungen reagiert, aber dabei das Ganze im Auge hat.
Während früher der Markt auf längere Zeit berechenbar (ruhiges Gewässer) war, befinden wir uns heute in einem dynamischen Markt (Wildwasser). Wir brauchen daher lebendige Organismen (Organisationen), die rasch reagieren können.
10. Menschliche Prozesse
Die Menschen, die unmittelbar und täglich mit den Prozessen befasst sind, können diese am besten beurteilen. Denn nur sie sind in der Lage, diese zu analysieren und zu optimieren. Nur mit ihnen und durch sie kann es gelingen, Prozesse tatsächlich zu optimieren.
Das bedeutet aber nicht, dass es nicht der Vision und Umsetzungskraft einer Führungsperson bedarf. Das bedeutet auch nicht, dass man sich keine Beratung und Unterstützung von außen holen darf. Das bedeutet aber sehr wohl, dass Prozessoptimierung nur top-down nicht gelingen wird.
Die Unternehmenspyramiden müssen auf den Kopf gestellt werden. Die gesamte Unterstützungsorganisation ist Dienerin der Wertschöpfung. Es ist die Verantwortung der Führungskräfte, die optimalen Bedingungen für die Wertschöpfung zu schaffen. Nur lebendige Organisationen schaffen so etwas. Eine Pyramide, die auf der Spitze steht, muss hochdynamisch (lebendig) sein, um nicht umzufallen. Daher sind klassische Pyramiden auch Grabstätten für das Unbelebte. ;-)
11. Der Arbeitsplatz als entscheidender Erfolgsfaktor
Stellen wir uns eine Baustelle als Operationssaal vor: Alle Werkzeuge sind optimal vorbereitet, es herrschen perfekte Lichtverhältnisse, die Arbeitsplätze sind ergonomisch, es gibt klare Standards, alle Arbeitsschritte sind genau geplant, jeder hat seine Position und Aufgaben. Wenn in einer solchen Umgebung einmal etwas Unvorhergesehenes passiert, kann sehr schnell und kompetent darauf reagiert werden – muss es auch! In einem OP ist das unter Umständen lebenswichtig.
Was ich damit sagen will: Der Arbeitsplatz wird als Prozess- und Erfolgsfaktor weithin unterschätzt.
Man nehme einen Menschen, stelle oder setze ihn an einen Platz und sage ihm, was er zu tun hat. Oder man erkläre einer Gruppe von Menschen umfassend, worauf es ankommt, und lasse sie gemeinsam nicht nur die Prozesse, sondern auch ihre Arbeitsplätze entwickeln. Was ist wohl erfolgreicher?
12. Optimierung endet nie
Optimierung ist nie erledigt und kann in mehr oder weniger deutlichen Initiativen erfolgen. Im Kern handelt es sich aber um permanente, eher kleine Optimierungsschritte, die aus dem Team kommen und vom Management unterstützt werden müssen. Ganz falsch ist die Haltung, dass man nun optimiert habe und so fortfahren könne. Dann ist man morgen schon überholt. Daher ist es wesentlich, nach jedem Optimierungsschritt sofort wieder offen zu sein für den nächsten.
13. Offenheit und Mut zum Fehler
Ohne Offenheit und Mut zu Fehlern im Unternehmen, im Team, auf der Baustelle wird kein Geist der Optimierung entstehen. Denn wie soll man Fehler erkennen und ausbessern, wenn man sie nicht zugeben darf? Da schauen doch alle gleich lieber weg – nach dem ewigen Motto „das war immer schon so“ und „da kann man gar nichts machen“. Es ist die Aufgabe der Führung, eine Kultur der Offenheit zu schaffen und zu leben. Es braucht keinen Mut, Fehler aufzuzeigen und zuzugeben, wenn daraus Erfolg entsteht.
Wir müssen im Baugewerbe verstehen, dass wir nicht gegeneinander spielen, sondern in derselben Mannschaft und mit dem gleichen Ziel: Wir wollen ein Gebäude errichten.
Sämtliche Bereiche werden isoliert betrachtet: Entwicklung, Planung, Ausführung – hier sogar alle Gewerke getrennt – im Ausschreibeverfahren werden die billigsten Bieter zusammengewürfelt. Fehler anzusprechen und davon zu lernen braucht Vertrauen zu den Teamkolleg:innen und Wiederholung durch gemeinsames Üben! Die Strukturen am Bau sind das feindlichste Gebiet für eine offene Lernkultur. Fehler der anderen werden bewusst und mit hohem Aufwand gesucht, um daraus Profit zulasten Dritter, zulasten aller anderen, zulasten des Projektes zu schlagen.
Wir haben mit unserer Baulogistik der Waldviertler Handwerker bewiesen, wie leicht es sein kann, diese Wand zu durchbrechen und durch ein gemeinsames Wirksamwerden die Bauabläufe eklatant zu verbessern: bessere Qualität, schnellere Bauzeit, geringere Kosten, höhere Kundenzufriedenheit, höhere Mitarbeiterzufriedenheit, ökologischer – das müssen unsere Mindestansprüche sein.
14. Die gemeinsame Gruppensteuerung
Das Zentrum der Optimierungsarbeit ist die gemeinsame Abstimmung in der Gruppe, die Orchestrierung aller Maßnahmen. Sie erfolgt nahe am Prozess, inmitten des täglichen Geschehens, an einem eigens dafür eingerichteten Arbeitsplatz. In einem gut geführten Unternehmen hat Selbstverwaltung viel Raum – denken wir an den Kreisverkehr aus Punkt 4.
15. Administration, Überwachung, Reibung
Die IT wird oft in Zusammenhang mit Begriffen wie Administration und Kontrolle genannt. Mehr Kommunikation führe zu mehr Reibung. Tatsächlich hat die Digitalisierung Kehrseiten. Das ist ein sehr kontroversielles Thema und nur durch das klare Bekenntnis (samt der praktischen Umsetzung), dass der Mensch immer die Oberhand haben muss, lösbar.
Die IT ist Dienerin der Menschen und darf nur so verstanden werden.
Nicht der Mensch hat sich nach den Prozessen der IT zu richten, sondern die Menschen entwickeln ständig die Prozesse weiter und die IT hat sich an diesen zu orientieren!
16. Minutiöse Planung
Das Wort „minutiös“ steht hier richtig. Am Bau sind wir Zeitpläne im Wochentakt gewöhnt. LEAN-Management fordert uns jedoch minutengenaue Prozessplanung und -dokumentation ab. Diese zu erreichen und permanent weiterzuentwickeln, ist Aufgabe des Teams, und zwar gemeinsam mit der Team- und der Unternehmensleitung, die die Kultur und Strategie dazu schaffen.
Die gemeinsame Planung der Abläufe hat nur ein Ziel – ein gemeinsames Verständnis zu schaffen. Denn nur dadurch ist es möglich, Abweichungen vom Plan an die Oberfläche zu bringen und an der Weiterentwicklung zu arbeiten. Je genauer der Prozess beschrieben ist, desto besser kann er weiterentwickelt werden. Dazu wieder ein Beispiel: Ich kann die Materiallieferung an eine Baustelle so beschreiben: „LKW abladen“. Ich kann sie aber auch so beschreiben: „LKW sucht Parkplatz, Fahrer steigt aus, Fahrer sucht Staplerfahrer, Staplerfahrer wird gerufen, Staplerfahrer kommt zu Entladeplatz, Lieferpapiere werden kontrolliert, LKW-Plane wird geöffnet, Material wird entladen, Material wird kontrolliert, Lieferschein wird im System gebucht, Material wird in das Regal eingelagert.“
Beide Beschreibungen handeln vom gleichen Prozess. Aber: In welcher Beschreibung ist wohl das Verbesserungspotenzial besser erkennbar?
17. Exakte Bedienung
Um einen Minutentakt einhalten zu können, braucht es exakte Vorleistungen und Bedienung des Teams vor Ort. Auch hier gilt wieder: Der Folgeprozess ist immer der Kunde. Der Kunde ist der König und entsprechend zu bedienen.
Diese „Bedienung“ des Prozesses umfasst die gesamte Vor-Portionierung, Vor-Logistik und exakte Anlieferung. Wir kippen nicht das Vormaterial irgendwo in der Nähe der Baustelle ab und die Monteure sollen sich zusammensuchen, was sie brauchen. Ganz im Gegenteil.
18. Hohe Ordnung
Natürlich ist auch hohe Ordnung Teil dieses Prinzips. Das reicht von der Ordnung bei eindeutigen, konsequenten Bezeichnungen für alles und jedes bis hin zur Ordnung im Werk und auf der Baustelle. Nur an einem ordentlichen Arbeitsplatz kann Qualität entstehen, da dadurch Abweichungen sehr schnell an die Oberfläche kommen. Oberstes Prinzip: Die Abweichung erkennen!
19. Optimierung ist übertragbar
Wir sind zu folgender Erkenntnis gekommen: Prozessoptimierung ist eine Leistung, ein Produkt und damit übertragbar. Die Optimierung von Prozessen hat grundsätzlich zwei Tangenten:
1. die fachliche – denn nur Prozesse, die man versteht und beherrscht, kann man optimieren.
2. die geistige, deren Ursprung bei Toyota zu finden ist.
So hat sich die Schrenk GmbH durch ihre Erfolge kontinuierlich weiterentwickelt:
- Zunächst haben wir uns auf Holz, Türen und Treppen fokussiert. So wurden wir zum Holz-Optimierer.
- Dann haben wir die Bedeutung der Prozesse für den Erfolg erkannt und verbessert. Wir wurden Prozess-Optimierer.
- Daraus entwickelten sich die Ideen für die Vorfertigung und Fertigteilhäuser. Das machte uns zu Objekt-Optimierern.
- Schließlich wurden wir immer öfter gefragt, wie wir das gemacht haben, und wir begannen, das Wissen weiterzugeben und wurden so zu System-Optimierern.
Wir schreiben das so plakativ, weil es zeigt, was alles möglich ist – aus einem KMU, aus einer peripheren Region heraus. Wir schreiben das so plakativ, weil es wichtig ist zu zeigen, dass der Erfolg nicht von der Größe abhängt.
20. Zusammenfassung am Ende
Wie so oft: Alles klingt so logisch, so einfach, wenn man es liest. Wie so oft machen andere dann eine Wissenschaft daraus. Wie so oft erkennen wir nicht, dass es um das Zusammenführen an sich einfacher Elemente geht.
Das Zusammenführen ist nicht gerade die Stärke der Baubranche, obwohl es eigentlich nur darum geht. Die Digitalisierung wird uns neue Wege des Zusammenführens eröffnen. Die Prozesse werden wir optimieren müssen, ob wir es LEAN nennen oder anders. Die Vorfertigung wird im Bauwesen Einzug halten.
Wie wir das zusammenführen, wird weisen, wie erfolgreich wir sind – im Waldviertel oder am Weltmarkt.
Kein Artikel dieser Welt kann beschreiben, was man in Vitis, in unserem Unternehmen, erleben kann. Darum haben wir mit der „DeepLean Lernstatt“ einen Raum geschaffen, in dem man hautnah anhand von Simulationen die Welt des Lean-Managements erleben und im wahrsten Sinne des Wortes „begreifen“ kann.
Wir haben erkannt, was Lean ist – nicht nur die Werkzeugkiste mit Tools im klassischen Ansatz, sondern die Kultur, die Einstellung, der Fokus auf Menschen sowie die Idee und der Gedanke, gemeinsam das Bestmögliche erreichen zu können. Es ist eine Mischung aus Geduld, Fleiß, Hingabe, Scheitern, Ausdauer und Kreativität. Wir sind noch lange nicht am Ziel, wir werden weiterlernen und Fehler machen. Ich freue mich darauf!
Der Text wurde ursprünglich von Hon.-Prof. Dipl.-Ing. Dr. techn. Wilhelm Reismann, Präsident des österreichischen Ingenieur- und Architektenvereins, nach einem Interview mit Stefan Schrenk verfasst. Wir veröffentlichen hier eine leicht überarbeitete Fassung.